Proyecto: ELEMENT: CROR Engine debris Middle level Impact and Mechanical test.
- Inicio
- Investigación y transferencia
- Investigación en la UC3M
- Proyecto: ELEMENT: CROR Engine debris Middle level Impact and Mechanical test.
Summary of the context and overall objectives of the project (For the final period, include the conclusions of the action)
- This section should include information on:
- What is the problem/issue being addressed?
- Why is it important for society?
- What are the overall objectives?
The European Union (EU) aeronautic industry is a world leader in its sector, and contributes to the EU economy with more than 500000 jobs and with a turnover of close to 140 B€. Regarding the production of civil aircraft, EU companies have, right now, about the 40% of the global market of short/medium range aircrafts. The competition in this huge market from new countries is starting to increase and hence, in order to maintain (or if possible increase) that portion of the global sales, it is necessary to being leaders in innovation and in product performance. The objective of the Clean Sky 2 program is to build a platform to potentiate the innovation in this important industry for the EU. Inside the Clean Sky 2 program there are 6 different technical areas called, three Integrated Technology Demonstrators (ITD) and three Innovative Aircraft Demonstrator Platform (IADP); the present proposal is focused in the Large Passenger Aircraft (LPA) IADP.
Fuel consumption is probably the most important factor in the civil aircraft industry, and almost all the innovations are focused in this subject, always without compromising the security. Lower fuel consumption not only means lower operating cost of the airlines, but also lower CO2 emissions. The challenge proposed in this program is to address technologies that could allow achieving a 20% in specific fuel consumption; it is expected that these innovations could be introduced in the aircraft with market entry between 2025 and 2030.
One of the most promising technologies that could allow achieving the aforementioned goal is the Counter Rotatory Open Rotor (CROR) engine, which could offer an improvement in fuel consumption in the range of 15% - 20% compared to the actual engines. The best position for the CROR engines is in the aircraft rear-end; this is due to the large diameter of those engines, and also to provide additional advantages such noise cabin reduction and passenger comfort. The location of the engine at the rear of the fuselage is a very important engineering challenge, since its integration implies several important changes of the aircraft structure. Some examples are the large pylon that has to be designed to support the structure that could induce vibration and fatigue in the rear of the fuselage, the modification of all the systems because of the new location, the modification of the aircraft centre of gravity...etc.
In addition of all this new issues that have to be addressed, there is a very important one which is the tolerance to the engine failure. In particular, the topic of this project is focused in blade release or an Uncontained Engine Rotor Failure (UERF); under these circumstances high energy debris could impact to the fuselage, causing large structural damages that could compromise the aircraft structure safety. The current proposal is focused in the development and maturation of innovative shielding solutions to sustain high and low energy debris associated with the engine failure.
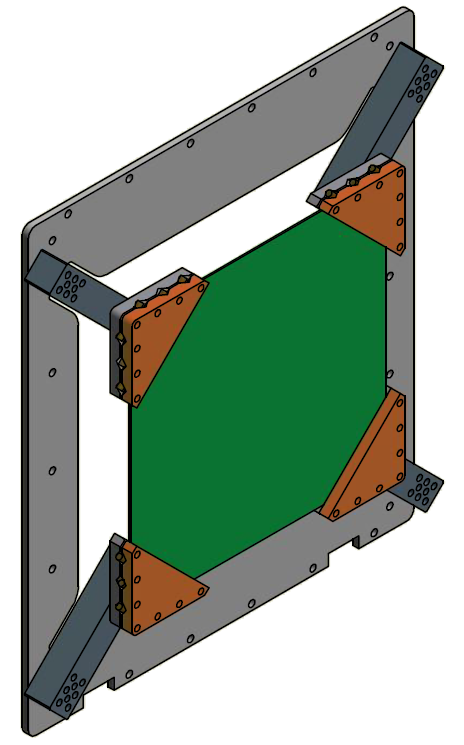
There are two overarching objectives in this project. The first one is to validate the maturity level of different technologies and structural solutions, to protect the rear-end structure from different impacts associated to engine failure. To this end both real and virtual impact tests of debris associated with the engine failure will be performed on both simple panels and full-scale representative aircraft structures.
The second objective of this project is to advance in the development of virtual testing methodologies. The economic impact of performing real experimental tests for the aircraft companies is very high, and virtual testing could diminish the number of experimental test (and hence its economic impact), which ideally could be limited to the ones that allow the aircraft certification. Right now the virtual testing technique is widely used in static problems, but its application under dynamic (impact for instance) conditions is limited. This project will allow improving the virtual testing for impact problems, increasing the competitiveness of the EU aircraft companies.
One of the most critical challenges of such innovative engines mounted on the rear fuselage is safety, in accordance with the certification requirements in the case of failure. Damage to the airframe from a failed blade could potentially be catastrophic. High energy debris can be released and impact the aircraft at high speed, challenge the structure integrity and the safe continuation of flight and landing, endangering passenger’s life. Safety of crew and passengers is of highest importance, which is reflected in strict regulations and requirements of the aviation authorities that need to be met by the aircraft manufacturer.
The aviation regulatory agents have been engaged in discussions with airframe and engine manufacturers concerning regulations that would apply to new technology fuel efficient “open-rotor” engines. Existing regulations for the engines and airframe did not envision features of these engines that include eliminating the fan blade containment systems and including two rows of counter-rotating blades.
Therefore, the feasibility of using aircraft fuselage shielding needed to be investigated and this project deals in part with this lack of documentation regarding to certification specifications, acceptable means of compliance and guidance material (for use in the certification process).
All experience gained during the tasks carried out in the project will support the definition of an aeronautical product testing framework as part of the validation and certification process of the development of new technologies resulting from the integration of the advanced new engines and propulsion concepts, such as CROR, in new eco-efficient aircraft generation
Work performed from the beginning of the project to the end of the period covered by the report and main results achieved so far (For the final period please include an overview of the results and their exploitation and dissemination)
The main objective of this project is to validate the maturity level of different technologies and structural solutions, to protect the rear-end structure of a civil aircraft from different impacts associated to engine failure. The project defines two steps in approaching to this problem. The first one (level 1) considers small flat panels in order to compare different shielding solutions, whereas in the second one (level 2) full scale aircraft structures will be contemplated in order to validate the shielding solutions selected in level 1 phase. In this first period (first 18 months) the level 1 step has been almost concluded; the level 2 has been started but no experimental test has been performed up today.
The first part of the work has focused in preparing the experimental set-up for the experimental tests; this was a hard work since two different projectiles have been used (CFRP prism fragment and a steel sphere) and also different rig setup has been developed for monolithic, nets and dry fabrics shields. At the same time numerical simulations have been performed to analyse the best boundary conditions for the shielding considered.
The main part of this level 1 step has been the experimental test performing. Almost 300 high velocity impact tests have been accomplished, considering different shielding solutions. For every test the impact energy absorbed has been measured; in addition, three high speed video cameras were used generating a huge quantity of data for every test. Some of the configurations tested are very promising in terms of protection capacity and low weight.
Progress beyond the state of the art, expected results until the end of the project and potential impacts (including the socio-economic impact and the wider societal implications of the project so far)
The CROR engines seem to be the best option in order to increase the fuel efficiency and the economics of the commercial civil aircraft for low and medium range. The use of this engine presents many challenges to the engineers, because of its position in the rear-end, which will promote many modifications regarding the different systems. One of the main objectives of this project is to validate the maturity level of different shielding solutions to protect the rear-end against the impact of both blades and debris in case of engine rotor failure. Once validated, the path to adopt these new engines will be much clearer, since the protection of the fuselage is one of the key factors. It is possible to state then that the impact of the conclusions of this project will be very important and also will have important consequences on the rest of the program to adopt the CROR engines. It is worth mentioning also that the TM, with the conclusions extracted from this project, will support aviation regulators to define and determine the new certification requirements that will be applied to the new generation of engines to be installed in the rear fuselage to ensure structural integrity and safety in case of engine failure.
Another important objective of this project is to develop a virtual testing methodology to predict the behaviour of complex structures. Numerical models are usually validated with experiments performed on small specimens. Sometimes this validation could not be easily extrapolated to large structures such aeronautics ones; a representative aeronautic structure will include metallic frames, composite stringers and metallic joints between the different elements. In this project the numerical methodology will be validated with both simple specimens and complex structures (L1 and L2 tests). In addition, two different types of impactors will be used (metallic and composite fragment) which will add more generality to the virtual testing methodology. With this large test campaign, it is possible to state that a very reliable virtual testing tool will be obtained for modelling the high velocity impact of fragments on aeronautic structures. This tool will positively impact on the economics of the future developments for the TM, since the number of test for other high velocity impact analysis will be considerably reduced. These kinds of advances are key to increase the competitiveness of the European aeronautic sector.
The UC3M will dramatically increase its capacity of performing high velocity impact tests with the new launcher that will be one of the largest ones along Europe. This upgrade will help to increase the work load of the laboratory which, in the future, could allow the creation of a spin-off which will exploit the laboratory capacities and create new jobs. Spain has a very important unemployment problem, and the possibility to create highly skilled jobs is very important for the Spanish society.
Apart from the impact of achieving the two main objectives it is important to mention other potential spin-off impacts. One is for the Vázquez y Torres Ingeniería SL (VTI) company (one of the partners of this proposal), since the development of a large experimental device will add some skills to its capacities, which could later be used for other projects, increasing its portfolio of products. This company will increase its competitiveness in the field of experimental setup developing for the aeronautic and aerospace industries.
VTI is an engineering company with a large experience in the design and supply of special test systems and particularly with regard to high speed impact testing facilities and equipment necessary to perform the required mechanical tests to validate shielding solutions. VTI has manufactured different types of high velocity gas actuated projectile launchers (pneumatic launchers). The actual need to investigate the viability of using aircraft fuselage shielding in the new generation of eco-efficient aircraft because of the introduction of a new concept of power plant requires having the appropriate experimental facilities to support the validation of new developed shielding solutions. VTI´s background experience on pneumatic launchers, in terms of speed range (up to 275 m/s), maximum energy (up to 300 KJ), gun barrel diameter (up to 250 mm) and the design and development of its own high speed triggering/shooting system converts this project and its objectives in a challenge and an opportunity:
-To take part in the achievement (upgrade and modifications required) to carry out the experimental testing described above, will provide us with new research capabilities to improve the pneumatic launcher and particularly be able to use it in a real and completely new scenario in which new certification requirements are still to be determined.
-To increase our competitiveness in the field of experimental setup developing for the aeronautic and aerospace industries, taking into account that this new generation of high energy impact debris testing will be needed in a short time frame.